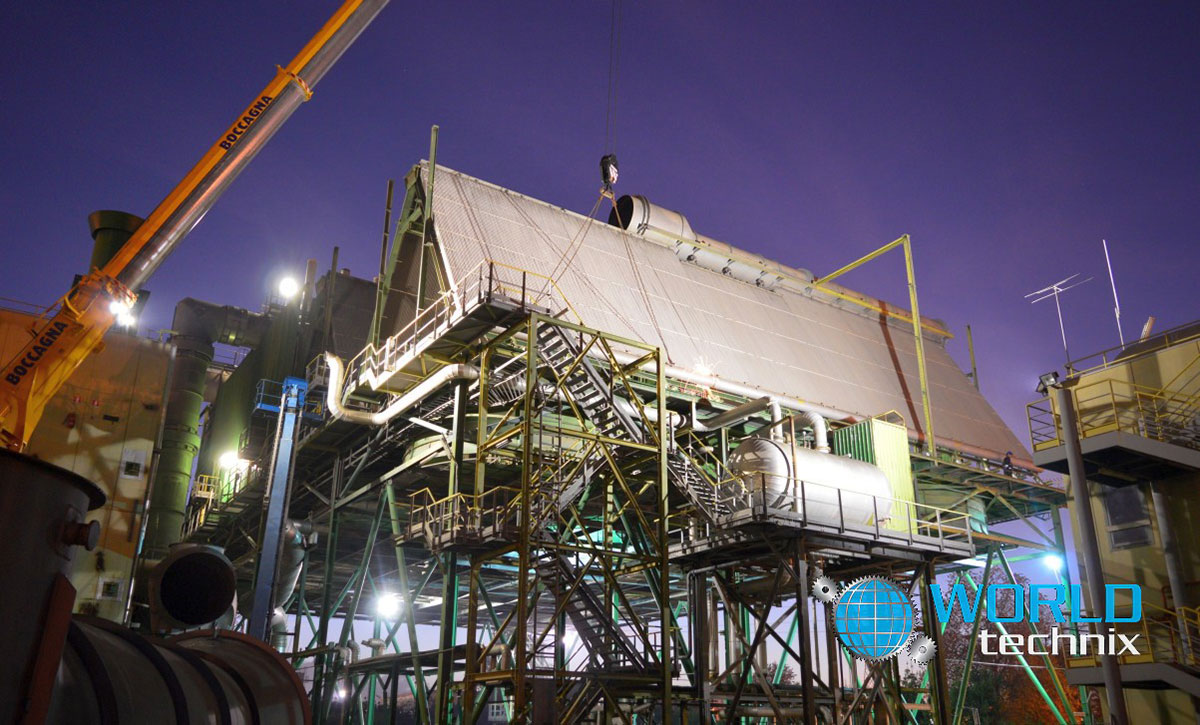
Przed podjęciem decyzji o relokacji maszyn i linii produkcyjnych zakładu przemysłowego warto wiedzieć jak cały proces przebiega oraz trzeba mieć świadomość, że wybór właściwej firmy, która przeprowadzi całą operację, jest tutaj najważniejszy dla powodzenia całej operacji. Proces relokacji maszyn czy całych linii produkcyjnych jest skomplikowany i wymaga ogromnego zaangażowania środków oraz doświadczonej kadry. Tylko nieliczne firmy decydują się na przenoszenie wyposażenia hali produkcyjnej lub przemysłowej „na własną rękę”. Dlaczego? Przede wszystkim dlatego, że wymaga to specjalistycznej wiedzy oraz wspomnianego już doświadczenia. Ponadto musimy dysponować nowoczesnymi pojazdami, maszynami oraz oprzyrządowaniem – to absolutna podstawa do tego, aby wspomniany proces został zrealizowany prawidłowo.
Wybór firmy specjalizującej się relokacji maszyn
Relokacja maszyn i linii technologicznych i to ogromna odpowiedzialność. Czasami wystarczy popełnić pozornie błahy błąd, aby doprowadzić do zniszczenia konstrukcji wartych kilka milionów. Właśnie dlatego ogromne znaczenie odgrywa prawidłowy wybór wykonawcy. Należy postawić na firmę, która już od lat działa w branży. Ponadto warto jest przeanalizować opinie wystawione przez poprzednich klientów, gdyż mogą nam one sporo powiedzieć o standardzie świadczonych usług. Decyzji o podpisaniu umowy nie należy podejmować zbyt pochopnie. Konieczne jest zweryfikowanie, jak wygląda kwestia odpowiedzialności za przenoszone mienie. Ubezpieczenie powinno pokrywać wszelkie potencjalne straty, które mogą powstać na skutek błędu fachowców. Nie można również wykluczyć uszkodzenia elementów podczas demontażu, czy też transportu. Oczywiście stawiając na renomowane przedsiębiorstwo ryzyko zaistnienia nieprawidłowości znajduje się na bardzo niskim poziomie, jednak należy być przygotowanym na każdą ewentualność.
Więcej informacji na temat usług relokacji maszyn i linii przemysłowych udzielą pracownicy firmy Worldtechnix.
Etapy relokacji fabryki
Relokacja fabryki składa się z wielu etapów. Nie można jednoznacznie powiedzieć, ile czasu potrzeba na jej przeniesienie, gdyż jest to kwestia bardzo indywidualna. Przed nawiązaniem współpracy z usługodawcą dobrze jest poprosić o wstępną wycenę, a także oszacowanie kosztów oraz określenie orientacyjnego terminu. Nic nie stoi na przeszkodzie, aby porównać kilka ofert, a następnie wybrać najkorzystniejszą. Pamiętajmy jednak o tym, że cena nie powinna znajdować się na pierwszym miejscu. Najważniejszy jest wysoki standard usług.
Proces relokacji fabryki można podzielić na trzy podstawowe etapy:
- Demontaż linii technologicznych oraz maszyn – często posiadają one duże gabaryty, a więc w zdecydowanej większości przypadków nie ma możliwości ich transportu bez wcześniejszego rozłożenia na części. Demontaż maszyn wymaga oznakowania komponentów, a także kompleksowego zabezpieczenia. Wiadomym jest, że łatwo o zgubienie drobnych części.
- Transport – wymaga fachowego zabezpieczenia ładunków przez zaginięciem, kradzieżą, czy też uszkodzeniem. Nie zapominajmy, że niektóre części są wyjątkowe delikatne, a więc relatywnie łatwo doprowadzić do ich zniszczenie.
- Ponowny montaż maszyn i linii produkcyjnych – po dowiezieniu ładunków na miejsce konieczne jest złożenie konstrukcji oraz przygotowanie ich do pracy. Dość często wymagają one prac konserwacyjnych, które polegają na usunięciu powstałych usterek.
Relokacja maszyn jest procesem wymagającym odpowiedniego planowania, realizacji oraz dbałości o bezpieczeństwo pracowników i maszyn.
Kluczowe aspekty, na które należy zwrócić uwagę, to:
rozpoznanie potrzeby relokacji maszyn i korzyści wynikających z tego procesu,
zaplanowanie relokacji maszyn, uwzględniając wszystkie etapy procesu,
wybranie odpowiedniego podmiotu wykonawczego oraz świadomość czynników wpływających na koszt usług relokacji,
zabezpieczenie maszyn podczas transportu oraz bezpieczne przetransportowanie i montaż maszyn,
zapewnienie bezpieczeństwa pracowników zaangażowanych w proces relokacji maszyn.
Przestrzeganie tych zasad pozwoli na skuteczną i bezpieczną relokację maszyn, minimalizując ryzyko uszkodzeń oraz przestoje w produkcji.